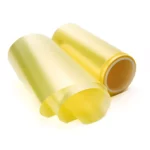
Brightness Enhancing Film
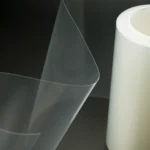
Polyester Printing Film
Description
The hard-coating process is a process in which paint or coating materials are evenly coated on the surface of the substrate. The basic principle is to apply coating or coating material on the substrate through coating equipment, and dry or solidify it to form a uniform and smooth film. The advantage of the coating process is that it can achieve efficient and high-quality surface coating. The thickness and performance of the coating film can also be achieved by adjusting the coating equipment and coating formula.
After the PET cured film is treated, the ink is easier to adhere to and the printing effect is better. The anti-scratch ability is enhanced, and depending on the different needs of the product, the surface hardness can reach above 4H or higher.
This material is widely used in mobile phone screens, control panels, touch screens, LCD screens, external membrane membrane switch panels, LCD nameplates, LED and DVD screen protection, flat panel display surface maintenance, in-mold casting for household appliance casing processing, etc.
Kaixin PET hard-coating film is made of ultra-highly transparent PET film as a carrier, coated with a transparent hard-coating layer (or double-sided hard-coating layer). The hard-coating side has high scratch resistance, and the other side is generally smooth. Suitable for printing patterns. The hardness generally ranges from 1H to 4H, and special hardness can be customized. It can be widely used in gravure printing of electrical buttons, nameplate printing, etc. The thickness is between 0.125MM~0.35MM, single-sided and double-sided anti-scratch, anti-fingerprint, and anti-glare can be customized. The anti-scratch hardness can be customized for 2H~4H. Both sides can be covered with PE high-temperature resistant protective film.
PET Hard-coating Film And IML Process
PET hard-coating film refers to a PET film that has been hard-coating on the outer surface. After the film is treated, the ink adheres more easily and the printing effect is better. The anti-scratch ability is enhanced, and depending on the different needs of the product, the surface hardness can reach above 4H or higher.
This material is widely used in mobile phone screens, control panels, touch screens, LCD screens, exterior membrane switch panels, LCD nameplates, LED and DVD screen protection, flat panel display surface protection, and in-mold casting for household appliance casing processing. Wait. PET hard-coating film structure In order to improve the surface properties of the PET film, improve the adaptability of printing and the bonding force of the vacuum aluminum plating layer, corona treatment is usually used to increase the surface tension of the film. However, the corona method has problems such as timeliness. Especially in high-temperature and high-humidity environments, the film tension after corona treatment is easily attenuated. However, the chemical coating method does not have such problems, so it is favored by the printing industry and the aluminum plating industry. In addition, high barrier films and antistatic films can also be produced using the coating method.
Production Process:
- Base material: The optical film produced by the company uses PET base film as the base material.
- Surface treatment: Perform surface cleaning and other treatments on the PET base film before coating to improve the adhesion of the base material surface and facilitate subsequent surface coating.
- Coating and curing: The rotating patterned die roller will evenly apply the prepared formula solution on the surface-treated PET base film in the form of prismatic lines on the patterned die roller, and at the same time, it will be coated with UV irradiation. Layer solidification.
- Online detection: Through the observation room at the other end of the production line, the quality of the finished product during the circulation process is detected in real time.
- Rewinding: Gather the finished product into a roll. The roll needs to be rolled with polished paper and fixed at both ends with plates.
- Sample preparation: take samples of finished coils.
- Testing: Test the sampled finished coils.
- The finished coils are put into storage.
It Is Necessary To Conceptually Clarify The IML Process
- IML: IN MOLDING LABEL (no stretching, small curved surface, used for 2D products)
- IMF: IN MOLDING FILM (suitable for high tensile products, 3D products)
- IMR: IN MOLDING ROLLER (remove the film on the surface of the product, leaving only the ink on the surface of the product)
- The surface of IML products is a layer of hard-coating transparent film, with a printed pattern layer in the middle and a plastic layer on the back. Since the ink is sandwiched in the middle, the product can prevent the surface from being scratched and abrasion-resistant, and can maintain the color for a long time without fading
Processes
- Cutting: Cut the rolled film into square blocks with designed dimensions for printing and molding processes.
- Flat printing: Make a film net according to the required icons and text, and print the icons and text on the cut square block of film.
- Ink drying and fixing: Place the printed film Film square in a high-temperature oven to dry in order to fix the IML ink.
- Attach protective film: To avoid scratching the surface of the printed film during the positioning hole punching process, sometimes it is necessary to apply a single or double layer of protective film.
- Punch positioning holes: The thermoformed positioning holes must be punched accurately. The positioning holes for the shearing process sometimes need to be punched in advance.
- Thermoforming (high pressure or copper mold): After heating the printed film, use a high pressure machine or copper mold to form it in a preheated state.
- Cut the peripheral shape: Cut off the waste material of the formed three-dimensional film.
- Information injection molding: Place the molded film with the same three-dimensional shape as the front mold on the front mold, and injection mold the finished IML product.
- Textures can be completed: CD texture, brushed, matte, leather texture, wood grain, various 3D patterns, but because the outermost layer is made of film material, the texture has no tactile feel.
Features
- Double-layer hard coating, 4H pencil hardness
- Suitable for screen and UV printing
- Excellent impact resistance and wear resistance
- Excellent chemical resistance
- Excellent light transmittance
Applications
- Mobile phone screen, touch screen, LCD screen
- Instrument panel, control panel, membrane switch panel, LCD nameplate
- LED, DVD screen protection, flat panel display surface protection
- IMD/IML for electronic product casings
Technical Data Sheet
Typical physical properties | |||
Properties | Value | Unit | Test Method |
Physical properties | |||
proportion | 1.4 | g/cm³ | ASTM D792 |
Optical properties | |||
Transmittance | >90 | % | ASTM D1003 |
Haze | <2 | % | ASTM D1003 |
Mechanical behavior | |||
Tensile strength (TD) | 222 | Mpa | ASTM D882 |
(MD) | 217 | Mpa | ASTM D882 |
Elongation at break (TD) | 80 | % | ASTM D882 |
(MD) | 120 | % | ASTM D882 |
Thermal properties | |||
Molding Shrinkage (TD) | 0.35 | % | ASTM D1204 |
(MD) | 0.85 | % | ASTM D1204 |
Surface hardness | 1-4 | H | ASTM D2578 |
Note: This test is for reference only and is not an absolute application indicator. |