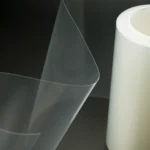
Polyester Printing Film
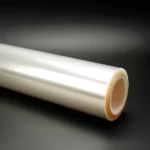
Silicone Release Film
Description
The diffusion film mainly consists of a three-layer structure, including the bottom anti-scratch layer, the middle transparent PET substrate layer and the top diffusion layer. The working principle of the diffusion film is that light is incident from the bottom anti-scratch layer, then penetrates the highly transparent PET substrate, and is then scattered by the diffusion particles dispersed in the diffusion coating to form a uniform surface light source. Most of the diffusion particles are spherical, and their function is similar to a convex lens. When the light passes through these particles, it is focused to a certain exit angle, thereby enhancing the brightness of the exit light. In addition, the particles of different sizes in the diffusion layer also ensure that light does not escape directly from the diffusion film, thus achieving an atomization effect.
In a backlight module, 1-2 diffusion films are generally required: bottom diffusion film (Bottom Diffuser) and top diffusion film (Top Diffuser). Among them, the lower diffusion film is close to the light guide plate and is used to convert the uneven light source emitted from the light guide plate into a uniformly distributed, blurred dot surface light source, and at the same time plays the role of shielding the light guide plate printing dots or other optical defects; the upper diffusion film is located The uppermost side of the backlight module has high light penetration capability, which can improve the viewing angle, increase the softness of the light source, and has the functions of diffusion and protection of the brightness enhancement film.
The purpose of the diffusion film is to uniformly convert linear light sources or point light sources into surface light sources. Its working principle is to use light to pass through media with different refractive indexes. The light produces many refraction, reflection, and scattering phenomena, causing optical diffusion effect.
In a backlight module, 1-2 diffusion films are generally required: bottom diffusion film (Bottom Diffuser) and top diffusion film (Top Diffuser). Among them, the lower diffusion film is close to the light guide plate and is used to convert the uneven light source emitted from the light guide plate into a uniformly distributed, blurred dot surface light source, and at the same time plays the role of shielding the light guide plate printing dots or other optical defects; the upper diffusion film is located The uppermost side of the backlight module has high light penetration capability, which can improve the viewing angle, increase the softness of the light source, and has the functions of diffusion and protection of the brightness enhancement film.
The purpose of the diffusion film is to uniformly convert linear light sources or point light sources into surface light sources. Its working principle is to use light to pass through media with different refractive indexes. The light produces many refraction, reflection, and scattering phenomena, causing optical diffusion effect.
Kaixin PET light diffusion film is mainly used in the backlight source part of LCD modules. When light passes through the diffusion layer with PET as the base material, it will pass through media with different refractive indexes, causing the light to undergo many refraction, reflection and scattering phenomena. The light can be modified into a uniform surface light source to achieve the effect of optical diffusion.
In the backlight structure, it mainly plays the role of correcting the diffusion angle, which increases the light radiation area, but reduces the light intensity per unit area, that is, reduces the brightness. After the luminous light source is diffused by the diffusion material, it can become a secondary light source with a larger area, better uniformity, and stable chromaticity. It has the function of diffusing light, that is, light will scatter on its surface, spreading the light softly and evenly; the basic structure of most diffusion films is to coat both sides of a transparent substrate such as PET with optical astigmatizing particles.
Main Material
- Polycarbonate Film
- Polyethylene Terephthalate Film
- Polymethyl Methacrylate Film
Production Process
- Substrate material: Diffusion film products use PET base film as the base material, and reflective film products use general white reflective film as the base material (hereinafter collectively referred to as PET base film).
- Surface treatment: Perform surface cleaning, corona and other treatments on the PET base film before coating to improve the adhesion of the base material surface and facilitate subsequent surface coating.
- Precision coating: Apply the prepared formula solution evenly on the surface-treated PET base film through the roller setting.
- Coating curing: Coating curing is carried out in the drying channel of the production line, mainly used for drying the surface of PET base film coating.
- Online detection: Through the observation room at the other end of the production line, the quality of the finished product during the circulation process is detected in real time.
- Rewinding: Gather the finished product into a roll. The roll needs to be rolled with polished paper and fixed at both ends with plates.
- Sample preparation: Take samples of finished coils.
- Testing: Test the sampled finished coils.
- Finished products: finished coils are stored in warehouse.
Main Functions Of Upper Diffusion Film And Lower Diffusion Film
Main Functions Of Upper Diffusion Film And Lower Diffusion Film |
||
Item | Upper diffusion film | Lower diffusion film |
Location | On top of the brightening film | between the BEF and the LGP |
Base material | Polyester film,PC film | Polyester film,PC film |
Haze characteristics | Small | Big |
Transmittance | Higher | Lower |
The main function | Protective function | Light diffusion function |
Anti-static | Yes | Yes |
Price | Higher | Lower |
Technical Data Sheet
Typical physical properties | |||
Properties | Value | Unit | Test Method |
Physical properties | |||
proportion | 1.4 | g/cm³ | ASTM D792 |
Optical properties | |||
Transmittance | 73 | % | JIS K 7136 |
Haze | 95 | % | |
Mechanical behavior | |||
Tensile strength (TD) | 180 | Mpa | ASTM D882 |
(MD) | 170 | Mpa | ASTM D882 |
Elongation at break (TD) | 125 | % | ASTM D882 |
(MD) | 120 | % | ASTM D882 |
Thermal properties | |||
Molding shrinkage TD) | -0.56 | % | ASTM D1204 |
(MD) | -0.85 | % | ASTM D1204 |
Environmental testing | Unit | Aging degree(△ YI) | luminance attenuation(%) |
High temperature/high humidity 250 hours | 85℃/85%RH | <0.1 | <1 |
High temperature 250 hours | 85℃ | <0.1 | <1 |
Low temperature 250 hours | -25℃ | <0.1 | <1 |
Thermal shock | (-25℃×1Hr-65℃×1Hr) ×100cycles |
<0.1 | <1 |
Note: This test is for reference only and is not an absolute application indicator. |