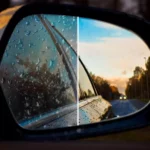
Anti-fog Film
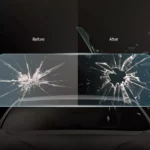
Explosion-proof Film
Description
Polycarbonate films can be decorated using a variety of printing types, including ink-jet digital, screen printing, and offset printing. The preferred method varies based on the customer’s print size, component geometry, print quality requirements and preferred film type. Among them, Kaixin’s polycarbonate digital ink printing film series is designed to improve the adhesion performance of digital UV ink when it comes into contact with lamination adhesives.
Kaixin’s ink printing films are available in polished and textured grades. Using polished film for digital printing will make the product more colorful and fuller of three-dimensional effect; using textured film for digital printing will make the product feel more noble and elegant. Therefore, digitally printed films can significantly improve product quality and added value of packaging.
Different printing technologies offer different advantages: Screen printing is the most commonly used printing technology for our films, which print directly on the media. This technology results in durable, long-lasting images with high opacity and color density, ideal for backlit printed films such as automotive dashboard components or electronic device keyboards.
Offset printing is ideal for high-speed, high-volume and relatively low-cost processes, such as designing complex security lines on ID cards; while digital printing is very flexible in terms of speed and volume because there is no need to set up a press and the technology can be used on demand Print in batches more than once.
UV ink screen printing has developed rapidly in high-end packaging products and optical disc printing due to its fast drying speed, no clogging of the screen, wide range of substrates, and excellent wear resistance, solvent resistance, and weather resistance.
Features and Applications
Features | Applications |
Excellent ink resolution and color display capabilities | Windows, display panels, etc. |
Ink adhesion is stable and firm | Strips/Numbers/Price Blocks |
The range of textures and consistent surface finish means no light will leak through the printed area | Various displays |
Excellent printing ability | Appliance labels |
Dimensional stability (excellent temperature resistance) | Decorative packaging materials |
etc. | etc. |
Analysis and solutions about the poor adhesion of UV ink on film
Commonly used films for making film printing materials include: polycarbonate (PC), polyethylene (PE), polypropylene (PP), polyester (PET), polyvinyl chloride (PVC), etc. But unlike paper, film is not absorbent, so film printing mainly uses UV embossed printing and UV flexo printing. In printing processing, a problem that label printing companies often encounter is poor adhesion of UV ink on the film surface. The reasons will be analyzed below and the troubleshooting methods will be explained.
Cause Analysis
The reasons for poor adhesion of UV ink on the film surface can be summarized as follows.
Poor UV ink curing
In actual printing processing, customers often encounter the situation that after UV ink is irradiated by ultraviolet lamp, the surface of the ink has been cured but the interior has not been completely cured. The binding force between the UV ink that is not fully cured and the film surface is relatively weak, and the ink layer is easily torn off the film surface when tested with tape.
The surface tension of the film is not enough for the post-printing process.
We know that corona treatment can increase the surface tension of film materials (such as PE/PP), but corona treatment is time-sensitive and will be affected by factors such as the storage environment and transportation environment of the material. Before printing, the operator should use a dyne pen or dyne liquid to check the surface tension of the film material. If the surface tension does not meet the requirements of the packaging machine, it will cause poor adhesion of the UV ink.
The UV ink used does not match
For some film materials, such as PET and BOPP, in order to improve their label printing suitability, material suppliers will add a coating layer to their surface. Since different UV inks use different types of resins, printing on the same coating layer will often show different results. If the UV ink used does not match the coating layer, there will be a problem of poor adhesion of the UV ink on the film surface.
Troubleshooting
In response to the above three situations, we propose the following solutions.
Determine whether the UV ink has been completely cured. We can use the thumb pressing method, that is, press the surface of the ink layer with your thumb firmly, and then press it back and forth several times. If there is ink stuck to your thumb, it can be determined that the UV ink has not been completely cured. There are many reasons why UV ink is not fully cured. It may be a problem with the ink itself or a problem with the UV curing system. The following two aspects should be noted.
① If the UV ink is not used up, be sure to close the lid of the ink tank and avoid light when storing. We know that ordinary sunlight also contains ultraviolet light, and UV ink will undergo chemical reactions after being exposed to sunlight for a long time , causing the ink to deteriorate. In addition, the ambient temperature where UV ink is stored should be around 20°C and should not be too high.
② The service life of UV lamps is generally about 1,000 hours. Some label printing companies often encounter situations where the UV lamp can still be lit after being used for more than 1,000 hours, but it can no longer fully cure the UV ink. This is because once the UV lamp reaches its service life, its spectral curve will change, and the ultraviolet rays emitted no longer meet the curing requirements of UV ink. Therefore, we should correctly record the usage time of UV lamps and promptly replace UV lamps that have reached the end of their service life.
Film label materials can be divided into two categories according to their printability: one type requires corona treatment before printing; the other type itself has been processed with a layer of coating that can be printed. For label printing companies, they should decide what kind of film material to purchase based on the capabilities of the printing equipment (such as whether there is a connected corona treatment device, etc.). Category 1 film materials can be purchased if the press has a corona treatment device. Before printing, the surface tension of the film material must be measured. If it is lower than 42mN/m, the label material must be subjected to in-line corona treatment before printing. This can ensure good adhesion between the UV ink and the film surface. If the purchased film material already has a coating layer that can be printed on the surface, the label printing company should consult the material supplier about which brand of ink should be used, because different coating formulas are suitable for different brands of ink. Only when the coating layer and UV ink match, can the problem of poor ink adhesion be solved.
To sum up, in printing processing, if we encounter the problem of poor adhesion between the film material and the UV ink used, we should correctly analyze the cause so that we can find the correct solution to the problem at the first time.
Technical Data Sheet
Typical physical properties | |||
Performance | Value | Unit | Test method |
Physical properties | |||
Water contact angle | 20±5 | ° | / |
Proportion | 1.2 | g/cm³ | ASTM D792 |
Coating adhesion | 5B | / | / |
Mechanical behavior | |||
Tensile Strength | 61 | Mpa | ISO 527-1 |
Elongation at break | 6 | % | ASTM D638 |
Bending strength | 92 | Mpa | ASTM D790 |
Flexural modulus | 2230 | Mpa | ASTM D790 |
Optical properties | |||
Transmittance | >89 | % | ASTM D1003 |
Haze | <1 | % | ASTM D1003 |
UV light transmittance 350nm | <1 | % | ASTM D1003 |
Thermal properties | |||
Molding shrinkage | 0.5~0.7 | % | ASTM D955 |
Microcard softening point | 148 | ℃ | ISO 306 |
Note: This test is for reference only and is not an absolute application indicator. |