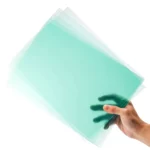
Composite Material
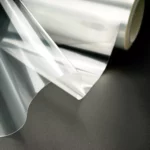
Full Fit Optical Clear Adhesive (OCA)
Description
Kaixin’s regular Optically Clear Adhesive ( OCA ) is a special adhesive used to bond transparent optical components (such as lenses, etc) . It is colorless and transparent, has a light transmittance of over 95%, good bonding strength, can be cured at room or medium temperature , and has small curing shrinkage.
Features
- OCA thickness 15um, 25um, 50um, 75um, 100um, 125um, 150um, 175um.
- Excellent optical properties/acid-free.
- Functional sheet materials have excellent compatibility (ITO, AgNW, etc).
- Plastic panels are easy to vent (PC/PMMA/ABS).
- Excellent adhesion to plastic and glass panels.
- Good step absorption performance.
- Excellent ink gap adsorption capacity.
- Produced in a high-cleanliness coating workshop.
Applications
- Touch screen – used for plastic panel lamination (P+F/P+G, etc).
- Vehicle/industrial control/home appliance plastic TP lamination.
- Suitable for various films and screens around the display of fixed mobile machines (glass screens, touch screens, etc).
Common problems and solutions
●Light Leak
Solutions:
① The customer’s own design size is the lower limit and the production size is lower than the lower limit, resulting in a smaller mold size design. You should communicate with the customer in advance to understand the actual size of the customer’s product.
② If there is a discrepancy between the supplier’s internal measurement and the customer’s measurement, you can take 10 products to the customer to measure the size, then take them back to the supplier to measure the size, compare the size difference between the two sides, and create a unified size standard.
③ Control the temperature of the processing environment, storage environment and transportation environment to control problems such as gum shrinkage.
●Problems such as creases, indentations, glue wrinkles, scratches, etc.
Solutions:
① If the roll core is too small, wrinkles and other defects may occur in parts close to the roll core. Use a 6-inch larger roll core instead.
② If the raw material is placed on the pallet, the weight of the raw material will cause indentation on the material. Use a jig to place the material in the air.
③The knife mold is not sharp enough or the foam is inappropriate, causing indentations. The knife is made of high-quality mirror knife (imported from Japan) wooden knife mold. The required thickness of the board is 21 – 22mm, which is 2mm thicker than normal. The foam is made of low-density and high-elasticity foam , generally with a density of 45° and an elasticity of 70%.
④ When the raw materials are cut, problems such as scratches and indentations on the surface of the material will occur. When the raw materials are cut, a light release film needs to be added for effective protection to avoid surface scratches. In addition, when slitting, pay attention to the material tension to minimize glue wrinkles.
⑤ Problems caused during die-cutting, reduce the pressure of compounding, avoid direct contact with metal or other fixed non-rotating items during die-cutting, and add protective devices.
●Glue overflow
Solutions:
① The knife mold is not sharp enough or the foam is inappropriate, causing indentations. The knife is made of high-quality mirror knife (imported from Japan) wooden knife mold. The required thickness of the board is 21 – 22mm, which is 2mm thicker than normal. The foam is made of low density and high elasticity foam. Generally, the density is 45° and the elasticity is 70%.
② Glue the mold, apply release agent to the inside of the knife and the side of the foam to prevent the mold from sticking.
③ Waste discharge causes glue overflow. Change the waste discharge angle to speed up the die-cutting speed and reduce the pause time.
④ Manual packaging causes poor extrusion. Strengthen the proficiency of techniques and correct mistakes.
● White spots and foreign matter
Solutions:
① During die-cutting, the material generates static electricity during operation, which will absorb dust and foreign matter in the air. An ion fan is installed at the exposed position of the glue, and there is a filter behind the ion fan; at the same time, a dust-free baffle is installed at the exposed position of the glue for isolation and protection.
② Influenced by environmental factors, reduce the frequency of workers walking in front of the machine; add or replace FFU (high-efficiency filter) in the clean room.
● Pinholes and depressions
Solutions:
① If dust and foreign matter are caused during processing, an ion fan is installed at the exposed position of the glue, and there is a filter behind the ion fan; at the same time, a dust-free baffle is installed at the exposed position of the glue for isolation and protection.
② Dust and foreign matter are adsorbed on the laminating wheel, which causes the light release film to be dented when the film is replaced with a light release film. At the same time, it affects the product colloid. Add an ion fan; increase the cleaning frequency of the laminating roller.
③ Taking the product with too much force may cause indentation on the product. When packaging, pay attention to the force with which the product is taken and handle it with care.
●Bubbles
Solutions:
① During packaging, air bubbles are caused by peeling off the low-viscosity film of the base, and the accuracy and proficiency of the technique of peeling off the low-viscosity film are enhanced.
② If the raw materials have defective bubbles, please provide feedback to the supplier and ask for improvement.
③ Die-cutting produces bubbles. The knife pad foam should be low density and high elasticity foam. Generally, the density is 45 degrees and the elasticity is 70%.
④ If air bubbles are found after die cutting, use a high-pressure deaerator to degas.
Technical Data Sheet
Typical physical properties | ||
Item | Standard | Unit |
Glue thickness | 50(±5) | μm |
Physical properties | ||
180° peel force | >700 | gf/25mm |
Retentivity | >24hrs | H |
Light film tearing force | 3~8 | gf/25mm |
Heavy film tearing force | 10~30 | gf/25mm |
Optical properties | ||
Transmittance | ≥90 | % |
Haze | <1 | % |
Color difference | 96.79*~0.7*0.15 | L*a*6 |
refractive index | 1.48 | n/25℃ |
Note: This test is for reference only and is not an absolute application indicator. |