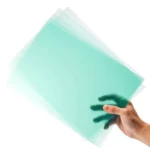
AG, AR, AF Coating For Optical Films
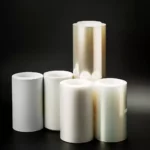
PET film in the printing industry
Polycarbonate, referred to as PC, has excellent properties in all aspects. Polycarbonate film or PC film is a film made from polycarbonate resin as base material
Polycarbonate films have a variety of detailed applications in the automotive field, mainly including the following aspects
Car windows: Polycarbonate film can be used in car side windows and sunroofs. It has high transparency and impact resistance, and can provide good visibility and safety for vehicles.
Car light covers: Because polycarbonate films have excellent high temperature resistance and optical properties, they are often used in car headlights and taillight covers to provide good light transmittance and protection.
Interior decoration: Polycarbonate film can also be used in car interior decoration parts, such as dashboards, center consoles, etc., to give car interiors good appearance and durability.
Film coating: Polycarbonate film can also be used as a car exterior film material to change the appearance color of the car or provide a protective coating to enhance the car’s beauty and durability.
Protective film: Polycarbonate film can be used as a protective film for automobile bodies, which can effectively protect the surface of the car body from scratches, stone hits and other factors.
Body markings: In automotive manufacturing, polycarbonate films are often used as substrates for body markings, graphics and signage, and their weather resistance and processability make them a widely chosen material.
Automotive glass interlayer: Polycarbonate film can be used as an interlayer material for automobile front windshields, providing impact resistance, explosion-proof and heat insulation functions to increase occupant safety and comfort.
To sum up, the applications of polycarbonate films in the automotive field are very diverse, covering many aspects such as body, interior, windows, lamps, etc., providing important support for automobile manufacturing and use.
Polycarbonate films with different functions are implemented in different processes in the automotive field. The following are some common process methods
Extrusion molding: used to produce products such as car windows and body protective films. The polycarbonate resin is put into an extruder, heated and extruded, and then cut into films of corresponding sizes after cooling.
Injection molding: Suitable for interior decoration parts, car lamp covers and other products, by injecting molten polycarbonate material into the mold in an injection molding machine, and forming a film or component of the desired shape after cooling.
Calendering process: used to produce products such as film coatings and car body logos. Polycarbonate resin sheets are placed in a calender and rolled into films or materials with specific patterns using the action of rollers.
Laminated glass process: The laminated material used to produce automobile front windshields is usually made by alternately laminating polycarbonate films and glass layers, and then subjecting them to high temperature and high pressure treatment to prepare the interlayer.
Hot press molding: Suitable for the production of interior decoration parts, body signs and other products. Under heating conditions, polycarbonate films are placed in molds for hot press molding to obtain products with the desired shape and surface texture.
Coating process: used to produce protective films, film coatings and other products. The polycarbonate material solution or molten resin is applied to the substrate through roller coating, spraying, etc., and a thin film is formed after solidification.
Vacuum forming: Commonly used to produce products such as car lamp covers, polycarbonate film is placed in a mold, heated and softened in a vacuum state, and then formed along the surface of the mold.
These process methods are designed to meet different application requirements, allowing polycarbonate films to have specific functions and properties and play an important role in the automotive field.
Flame-retardant polycarbonate has many important applications in new energy vehicles, mainly reflected in the following aspects
Battery casing: Flame-retardant polycarbonate can be used as casing material for new energy vehicle batteries. Due to its good flame-retardant properties and mechanical properties, it can provide protection for battery components and meet the lightweight and safety requirements of electric vehicles. Require.
Charging pile components: Among the components of new energy vehicle charging piles, flame-retardant polycarbonate is also widely used to manufacture shells, connectors and other components to ensure the safety and stability of charging equipment.
Electrical connectors and sockets: Flame-retardant polycarbonate can be used to manufacture electrical connectors and sockets for new energy vehicles. It has excellent insulation and flame-retardant properties and can ensure the safe operation of electrical systems.
Car interior decoration parts: Flame-retardant polycarbonate is also widely used in interior decoration parts of new energy vehicles, such as making dashboards, center consoles and other components to provide higher safety inside the car.
Cooling fan blades: Flame-retardant polycarbonate can be used to manufacture cooling fan blades for new energy vehicles. It can withstand high temperatures and has good mechanical properties, helping to maintain a stable operating temperature of electric vehicles.
Electric vehicle charging pile casing: Flame-retardant polycarbonate is also used to make the casing of electric vehicle charging piles, providing protection and aesthetics while ensuring safety.
Power battery heat sink: Since the power battery of new energy vehicles needs to dissipate heat to maintain the operating temperature, flame-retardant polycarbonate plays an important role in manufacturing heat sinks.
Electric vehicle exterior coverings: Flame-retardant polycarbonate is used to manufacture electric vehicle exterior coverings, such as body shells, electric control boxes, etc., to provide flame retardant properties and mechanical strength.
These applications highlight the diverse applications of flame-retardant polycarbonate in new energy vehicles and provide key support for the safety, lightweight and efficient performance of new energy vehicles.