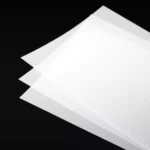
Opaque PVC Film
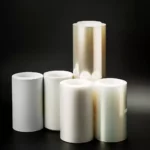
Silicone-free Release Film
Acrylic film is a film material usually made of polymethylmethacrylate (PMMA). It has the characteristics of high transparency, excellent gloss and weather resistance, and is often widely used in billboards, promotional signs, automobile signs, home decoration, industrial manufacturing and other fields. In different fields, acrylic film can exert its excellent appearance and durability.
Features:
High Transparency and Gloss: Acrylic film has excellent transparency and gloss, making it ideal for manufacturing high-quality products.
Weatherability: The film has excellent weatherability, resisting the effects of UV rays, chemicals and climate change, making it ideal for applications outdoors or in harsh environments.
Ease of processing: Acrylic film can be processed through cutting, forming, printing and other processing techniques to meet different needs.
Acrylic film vacuum forming process :
Acrylic films can usually be manufactured through a vacuum forming process. During the vacuum forming process, the acrylic film is heated to the softening temperature, then covered on the surface of the mold, and vacuum suction is used to shape the film to the surface of the mold. This process enables the acrylic film to form a precise shape with the mold and maintain its high transparency and gloss. Vacuum forming technology is widely used in the manufacture of automotive parts, lighting, displays and other products.
During the vacuum forming process of acrylic film, the following steps are usually followed:
- Mold preparation
First, a suitable mold needs to be prepared to ensure that the mold surface is flat and meets the required shape specifications.
- Heated acrylic film
The acrylic film is placed in a heating device in a plate or roll form and heated until it softens and reaches a suitable molding temperature.
- Install acrylic membrane
The softened acrylic film is placed on the pre-prepared mold, making sure to cover the entire mold surface.
- Vacuum adsorption
Set up a vacuum system above the acrylic film and start the vacuum pump to generate negative pressure, making the acrylic film close to the surface of the mold while expelling air bubbles and achieving the desired shape.
- Cooling
After the acrylic film is formed, it needs to be cooled to ensure that it solidifies into the desired shape.
- Remove finished product
Finally, the formed acrylic product is taken out of the mold and undergoes inspection and subsequent processing.
In general, the acrylic film vacuum forming process can efficiently produce high-precision, high-transparency products and is therefore widely used in many fields.
During the vacuum forming process of acrylic film, you also need to pay attention to the following key factors:
- Control heating temperature
The temperature needs to be controlled when heating acrylic film to ensure that it softens but does not become excessively deformed or damaged.
- Ensure uniform vacuum suction
The vacuum suction needs to act evenly on the entire mold surface to ensure that the acrylic film can fully fit the mold and achieve the desired shape.
- Mold design and maintenance
Reasonable mold design can affect the quality and production efficiency of finished products. In addition, it is also important to maintain the mold regularly to ensure that the surface of the mold is smooth and flat to avoid damage to the finished product.
- Quality inspection and packaging
The finished product goes through a rigorous quality inspection process to ensure that the product meets specifications and is properly packaged and labeled to prepare it for subsequent transportation and application.
During the vacuum forming process of acrylic film, you may encounter some common problems. Here are some possible problems and corresponding solutions:
- Bubbles and imperfections
Problem: Bubbles or other defects appear on the surface of the finished product.
Countermeasures: You can reduce the generation of bubbles by improving the control of heating and vacuum suction, while checking the material quality and mold surface integrity.
- Uneven thickness
Problem: The thickness of the finished product is uneven, with regional thickness being too thin or too thick.
Countermeasures: Adjust heating temperature and time to optimize vacuum suction distribution to ensure that the material can evenly cover the mold and form the required thickness.
- Deformation and shrinkage
Problem: The finished product deforms or shrinks after cooling.
Countermeasures: Consider the shrinkage rate of the material when designing the mold, and reasonably control the temperature and cooling rate during processing to reduce deformation and shrinkage.
- Mold wear
Problem: Mold surface wear seriously affects the quality of finished products.
Countermeasures: Regularly maintain and repair the mold to ensure that the surface of the mold is flat and smooth to avoid affecting the finished product.
- Material waste
Problem: A lot of material is wasted in the manufacturing process.
Countermeasures: Optimize mold design, maximize material utilization, and recycle waste materials.
The above are some common problems that may be encountered during the vacuum forming process of acrylic film and their corresponding solutions. Effectively handling these issues can improve production efficiency and product quality, and ensure the smooth progress of the production process.