Trustworthy brand, over twenty years of experience
The membrane switch is an operating system that integrates key functions, indicating components, and instrument panels. It consists of four parts: panel, upper circuit, isolation layer, and lower circuit. When the membrane switch is pressed, the contacts of the upper circuit deform downward and make contact with the plate of the lower circuit. After releasing your finger, the contacts of the upper circuit bounce back, the circuit is disconnected, and the loop triggers a signal. The membrane switch has a rigorous structure, beautiful appearance and good sealing performance. It has the characteristics of moisture resistance and long service life. Widely used in electronic communications, electronic measuring instruments, industrial control, medical equipment, automobile industry, smart toys, household appliances and other fields.
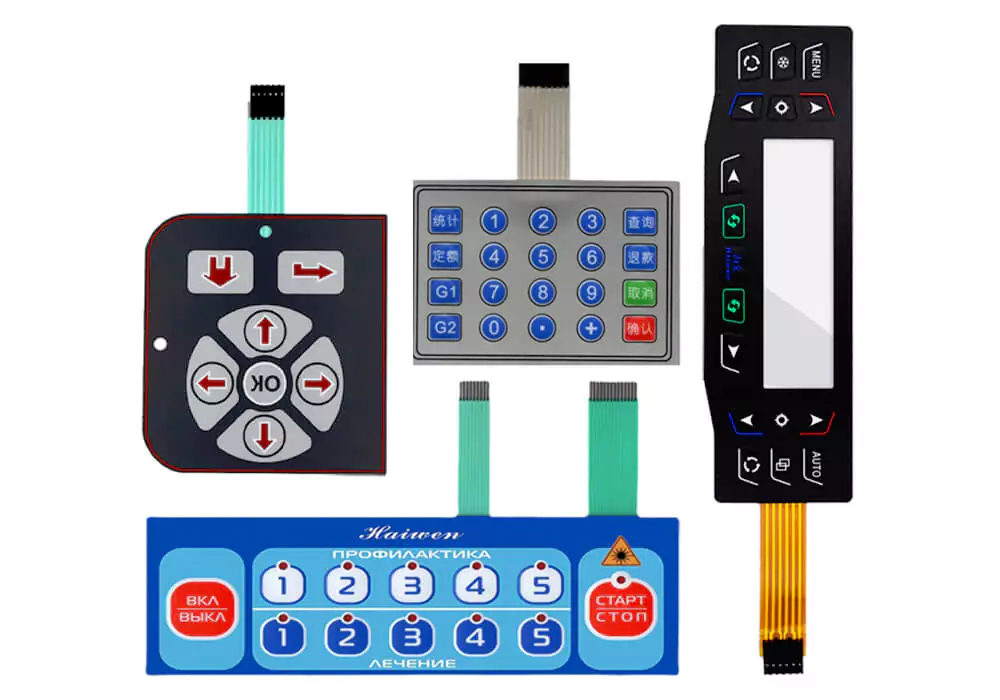
We Offer Three Main Materials
Stable to acids, alkalis and salts at room temperature. It has good wear resistance, flame resistance and self-extinguishing, noise and shock elimination, and good electrical insulation . Thermal stability is poor. Low cost ordinary signs and panels.
It has high light transmittance , low water absorption, good dimensional stability , excellent bending, tensile and compressive strength , excellent heat resistance, cold resistance, electrical insulation and atmospheric aging resistance. It has poor chemical resistance and fatigue resistance, and is prone to stress cracking. The output interface terminal circuit is generally printed with carbon material and has no protective coating. It is oxidized by the air and gradually forms a peeling layer, which eventually leads to circuit breakage. End of life, this is the most likely place for membrane switches to fail. It is mainly determined by the environment. Regardless of whether it is used or not, the physical damage time is 3 to10 years. The PC base material is degradable and is an environmentally friendly material. It is divided into sand surface and smooth surface. The thickness is generally 0.175 to 1.0 mm. The light transmittance of sand-surface PC reaches 78% and is suitable for digital tube displays. The high light transmittance of glossy PC is suitable for liquid crystal displays. It has good mechanical properties and is the most commonly used material.
It has good chemical resistance, is insoluble in general organic solvents, and is not resistant to alkali. It has excellent mechanical properties, electrical properties, rigidity, hardness and the largest strength and toughness among thermoplastics , low water absorption, excellent wear resistance and friction resistance, and high dimensional stability . The tensile strength is comparable to aluminum film and much higher than PC and PVC. The bulging of the keys feels better and is more durable. It is cheap and difficult to process into a matte surface, so textured PET is more expensive and is the most ideal substrate for making membrane switch circuits. Among them, textured PET is suitable for products with higher surface requirements or liquid crystal display windows.
Membrane switch production steps
- Substrate preparation
- Select substrate material: Polyester film, polycarbonate film and other materials are usually used as substrate.
- Cleaning the substrate: Use deionized water and organic solvents to clean the substrate to remove surface dirt and oil.
- Coating a conductive layer: Coating a conductive layer on the substrate, usually using silver paste or copper foil as the conductive layer.
- Graphical processing
- Photolithography: The designed graphics are projected onto a substrate coated with photosensitive adhesive, and the photosensitive adhesive is cured under ultraviolet irradiation to form a pattern.
- Development: Develop the exposed photosensitive adhesive in a developer to remove the unexposed portion of the photosensitive adhesive to expose the conductive layer.
- Metallization treatment: Metallization treatment is performed on the exposed part of the conductive layer, usually using nickel plating or gold plating to increase conductivity.
- Forming processing
- Stamping: Use a punch to punch the conductive layer on the substrate into the desired shape and size.
- Cutting: Use a laser or cutter to cut the substrate to the desired size.
- Bending: bend the substrate according to the design requirements to form the shape of the membrane switch.
- Assembly test
- Assembly: Assembling the membrane switch with other electronic components, usually using surface mount technology.
- Test: Test the assembled membrane switch, including tests on conductive performance, triggering force, lifespan and other aspects.
- Packaging: Pack the membrane switch that has passed the test and label the relevant information, such as model, specifications, etc.