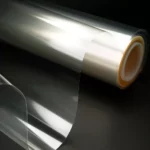
Optical Polyester film
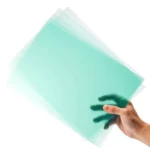
AG, AR, AF Coating For Optical Films
Why do home appliance panels use polyester film?
- Decoration and appearance requirements: Polyester film can provide a rich selection of colors, patterns and surface effects, which can be used to beautify the appearance of home appliance panels and increase the attractiveness and fashion of the product.
- Protective performance: Polyester film has strong wear resistance, pollution resistance and scratch resistance, and can effectively protect home appliance panels from damage by the external environment, daily use or cleaning processes.
- High temperature resistance: Some polyester films have good high temperature resistance and are suitable for home appliances that need to withstand a certain temperature, such as kitchen appliances, ovens, etc.
- Ease of processing: Polyester film is easy to process into various shapes and structures, and can be used to meet the panel design requirements of different home appliance products, such as flat panels, curved panels, etc.
- Environmental protection: Compared with other materials, some polyester films have good environmental performance and meet the environmental protection and health requirements of home appliances.
- By using polyester film, home appliance panels can achieve good decorative effects, high protection performance and excellent processing adaptability, meeting the multiple needs of modern home appliances for appearance, quality and functionality.
- Chemical resistance: Some polyester films have a certain tolerance to chemicals and can keep their surfaces intact during routine cleaning and maintenance, making them less susceptible to attack by chemicals such as detergents.
- Electrical insulation: Some polyester films have good electrical insulation properties and can be used as an insulation layer in home appliances to ensure the safety and reliability of the product.
- Lightweight and durable: Compared with traditional materials, polyester films are usually lighter in weight while providing sufficient strength and durability, which helps reduce the load on the product itself and extend its service life.
- Cost-Effectiveness: Polyester films generally have lower costs and are easy to process, helping home appliance manufacturers reduce production costs and increase production efficiency.
In what aspects is polyester film used in home appliance panels?
- Decorative panels: PET film can be used as a decorative material on the surface of home appliances. It can be given different patterns, colors and textures through printing, lamination and other processes, thereby improving the aesthetics and fashion of the product’s appearance.
- Protective panel: PET film can be used as a protective layer on the surface of home appliances, providing a certain degree of scratch resistance, wear resistance and anti-fouling functions, extending the service life of the product and keeping the appearance clean and shiny.
- Indicator panel: In some home appliances, PET film can be used as a covering material for the indicator panel, with indicator signs, button patterns, etc. printed on it to provide guidance and identification for product functional operations.
- Touch screen: In products such as smart control panels for home appliances, microwave ovens, refrigerators, etc., PET film can also be used as a touch screen material to support product interaction and human-machine interface design.
What kind of process is used for processing?
- Coating/printing: PET sheets undergo surface coating or printing processes to give them different decorative effects, patterns or functional coatings, such as anti-scratch, anti-fouling coatings, etc.
- Hot press molding: Put the coated or printed PET sheet into a mold, and perform hot press molding at a certain temperature and pressure to make it a panel with a shape and size that meets the requirements of home appliances.
- Subsequent processing: The formed PET film is subjected to subsequent processing such as cutting, folding, and punching to meet the design needs of different home appliances.
- Assembly: Assemble the prepared PET film panels and home appliances, including fixing, connecting and other steps.
How to print and heat press molding?
printing art:
- Surface treatment: PET film usually requires surface treatment before printing to improve ink adhesion and printing effect.
- Select printing technology: Choose the appropriate printing technology according to product design needs and requirements, such as flexographic printing, screen printing, digital printing, etc.
- Ink preparation: Prepare ink or ink that meets the requirements, including adjustment of parameters such as color, consistency, and drying speed.
- Printing: PET film is printed through printing equipment, and the required patterns or text are printed on the surface of the film.
- Curing/drying: After printing is completed, the ink is cured or dried to make it firmly adhere to the surface of the PET film.
Thermoforming process:
- Preheating PET film: Preheat the printed or coated PET film to increase its softening and facilitate molding.
- Put into the mold: Put the preheated PET film into the mold. The shape and texture of the mold need to match the requirements of the final product.
- Apply pressure and temperature: Use a hot press or hot pressing equipment to control the pressure and temperature of the PET film so that it softens under certain conditions and fully adheres to the mold surface.
- Cooling and solidification: After the molding is completed, the PET film is cooled to room temperature and solidified into a panel with the desired shape and surface properties.
Subsequent processing:
- Cutting: According to product design requirements, the formed polyester film is cut to fit a specific size and shape.
- Folding: If necessary, fold the edges of the film to facilitate subsequent installation and fixing.
- Punching/Slotting: According to the functional requirements of the product, the film is punched or slotted to install buttons, displays or other components.
Assembly:
- Component installation: Assemble the processed polyester film panels with corresponding electronic components, indicator lights, buttons and other components to ensure the reasonable layout and connection of each component.
- Connection and fixation: Use appropriate methods and materials to firmly connect and fix the components with the membrane panel, such as glue bonding, screw fixing, etc.
- Inspection and debugging: Conduct a comprehensive inspection of the assembled panels to ensure that each component functions normally and the appearance is intact.